we have been serving our clients by manufacturing all kinds of Rubber Rollers. As Rubber roller manufacturer, we design using high quality raw materials and sophisticated technology by our experienced professionals.
The selection of rubber Rollers depends upon the application. Our product line is made available in various sizes and dimension as needed by the customers. We advance rubber Industries a wide range of highly functional Rubber roller for their different application.
The reason for the degumming of the polyurethane rubber roller is that the temperature of the iron core and the mold should be close to the temperature of the polyurethane liquid during the polyurethane liquid casting process. When the temperature difference between the two is large, the curing speed of the constituent materials will be uneven, resulting in greater internal stress after the polyurethane material is cured. Mold planning and demolding requirements, mold planning and manufacturing, require better sealing, easy to close, open and demold.
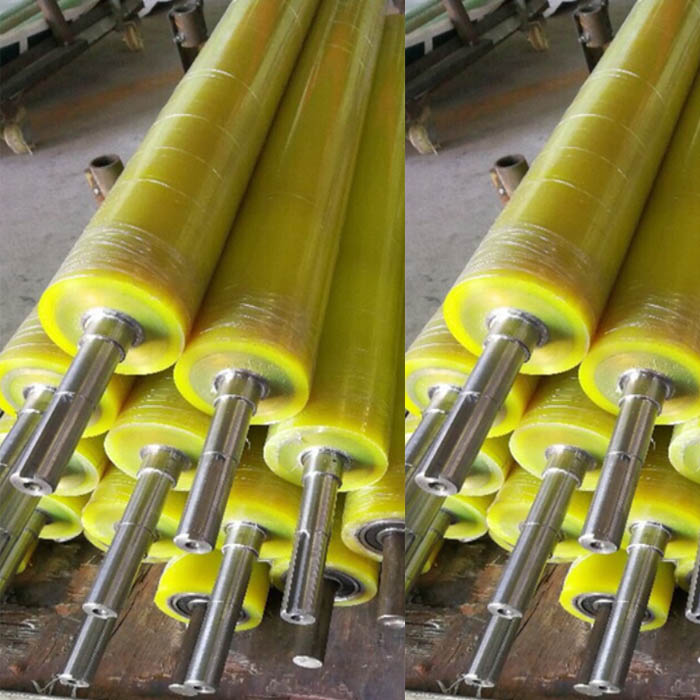

When planning the mold for the polyurethane rubber roller, the heat balance of the polyurethane must be considered, which is an important factor that is easily overlooked by the manufacturers. If the rubber roller is unevenly heated during the high temperature vulcanization process, the polyurethane vulcanization is generally incomplete at the junction of the iron core and the polyurethane, the elastomer strength is low, or there is a crack. The choice of adhesive is based on the theory of coordinative bonds. A coordinative bond can be formed between a polymer material with a large molecular weight and the surface of a metal material, so that the material and the metal can form a tight bond. Treatment of the iron core The treatment of the cast iron roll core is also one of the keys to the core removal of the rubber roller. To produce an outstanding combination of polyurethane elastomer and the iron core, the iron core generally needs to be cleaned, such as pickling to remove rust, using materials, etc., so that its appearance is clean and non-stained. Mechanical sandblasting is generally one of the methods for bonding strength. For polyurethane rubber-coated wheel processing, if it is a new rubber roller core, it is necessary to clean the oil on the surface of the iron core with a cleaning agent; if it is an old rubber roller core, it is necessary to clean the outer layer of the old rubber roller together. Clean the remaining glue on the surface of the iron core. The surface of the rubber roller core is roughened to the bonding area between the surface of the rubber roller core and the encapsulation. The rough-treated rubber roller core is sandblasted, and the sandblasting will be based on the material of the rubber roller core to select different types of sand for sandblasting. Sand blasting is to make the rubber roller surface rough, and the glue and the iron core can be bonded well after the rubber is encapsulated.
The rubber roller core after the polyurethane rubber roller treatment is encapsulated according to the customer's requirements. The rubber roller after encapsulation generally requires 10-15 hours of vulcanization time. After vulcanization, the core of the rubber roller and the rubber will be tightly bonded, and the rubber roller will be formed. Grind according to the size and shape required by the customer. When some customers have high requirements on the appearance of the rubber roller, they need to use a CNC grinder to polish the rubber roller mirror surface.
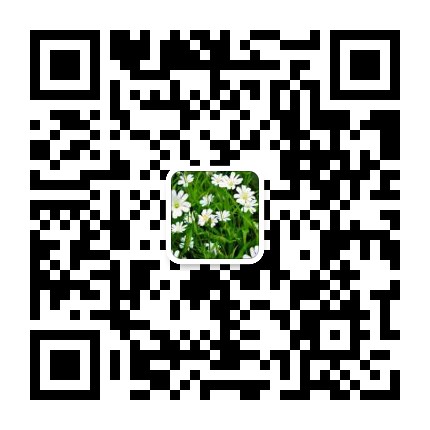
Post time: Oct-18-2021