The cold roll is a complex component with a very hard surface layer, which bears a lot of stress. Therefore, the cold roll requires high manufacturing quality, which is a necessary condition to ensure the effect of use.
The development of cold rolling rolls is driven by the pulling and roll manufacturing related technologies in the cold rolling industry. From the perspective of the needs of the cold rolling industry, the requirements for increasing wear resistance, roughness retention performance, accident resistance performance, uniformity and other indicators Increasingly high, the purpose is to achieve free rolling, rolling high-grade plates, reducing roll consumption, etc. Under the pull of these requirements, roll manufacturing enterprises are also making continuous efforts to improve and innovate roll manufacturing technology. The specific performance is as follows :
(1) The alloy composition of forged steel rolls continues to increase. The application of 5%Cr, 8%Cr, semi-high-speed steel, high-speed steel and other high-alloy steels on cold rolls is a trend. At the same time, the material of the rolls will maintain a variety of Adapt to the needs of different rolling conditions.
(2) Application of new roll blank composite manufacturing technology. In order to meet the requirements of high wear resistance of the roll surface and high comprehensive mechanical properties of the core, some manufacturers have been exploring electroslag casting, CPC, OSPRAY and other new surface composite technologies in the roll blank. Preparation on trial.
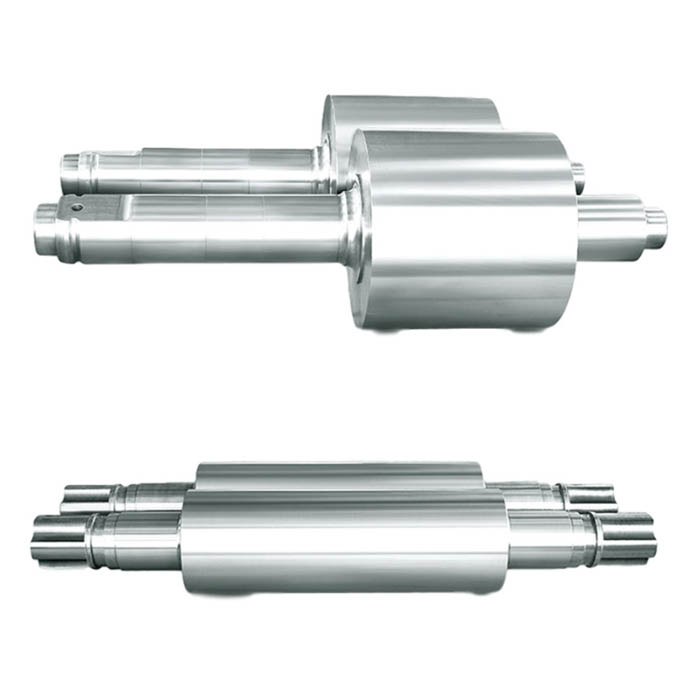
(3) Application of new roll heat treatment and processing technology. The application of large-scale CNC machine tools, the trial of computer-controlled heating furnaces and quenching equipment can increase the manufacturing accuracy and surface uniformity of the rolls, and meet the needs of high-grade rolling mills.
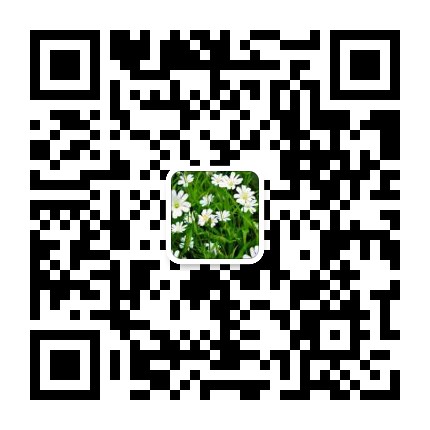
Post time: Mar-14-2022