At present, due to the continuous development of science and technology, the post-press finishing process is constantly innovating, and various new processes such as holographic positioning hot stamping and cold hot stamping have emerged. However, traditional hot stamping is an important process in post-press processing. In view of its unique luxurious decoration The effect was not neglected, but received more attention and preference from customers. Therefore, how to improve the quality of hot stamping has often become a problem that people discuss. The following will explain the operation of some hot stamping processes from several aspects.
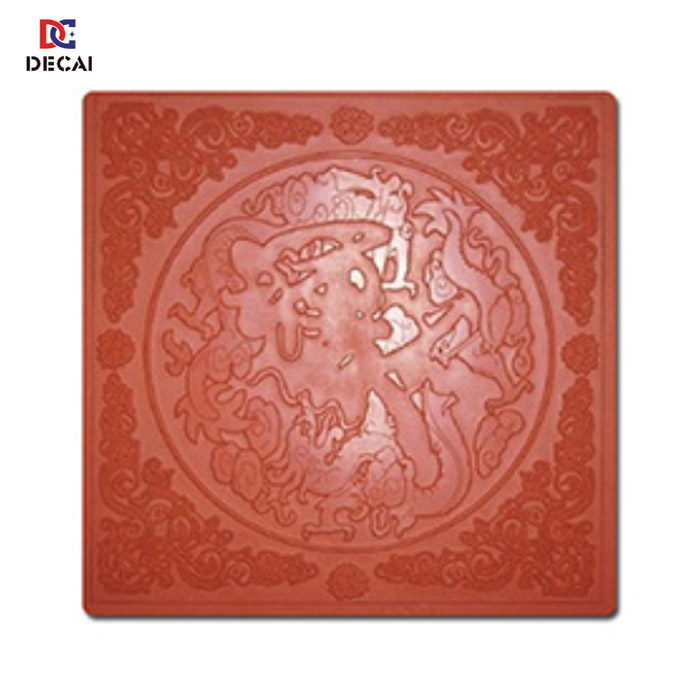
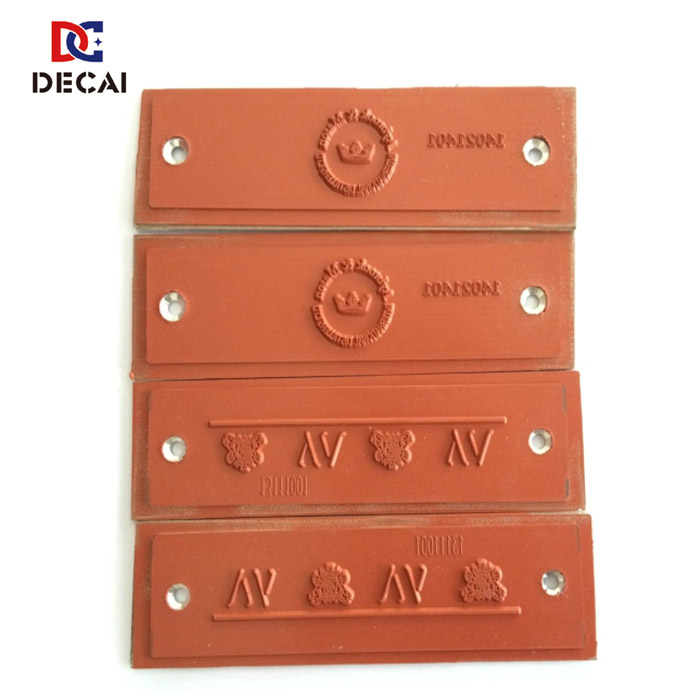
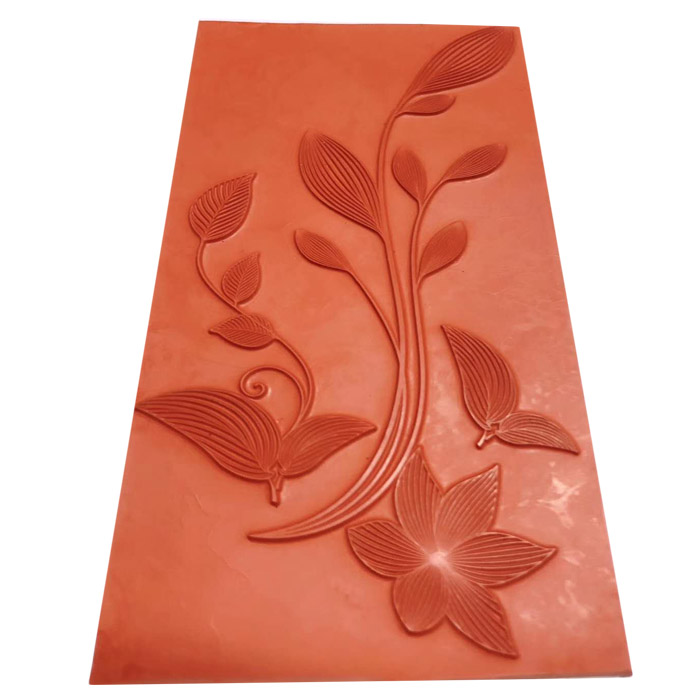
The basic process of bronzing
Basic process: First of all, in the state where the anodized aluminum is pressed by the hot stamping plate and the substrate, the anodized aluminum is heated to melt the hot-melt silicone resin layer and the adhesive. At this time, the heated and melted silicone The viscosity of the resin becomes smaller, and the viscosity of the special heat-sensitive adhesive increases after being heated and melted, so that the aluminum layer and the anodized aluminum base film are peeled off and transferred to the substrate at the same time.
As the pressure is released, the adhesive rapidly cools and solidifies, and the aluminum layer is firmly attached to the substrate, completing a hot stamping process.
Process flow: hot stamping preparation - plate loading - pad plate - adjustment of hot stamping process parameters - trial hot stamping - signature - formal hot stamping.
The way to improve the quality of bronzing
From the basic process of hot stamping, it can be seen that the three basic elements of hot stamping are: temperature, pressure and hot stamping time.
In order to obtain the ideal hot stamping effect, process parameters such as hot stamping temperature, hot stamping pressure, and hot stamping speed must be reasonably mastered; in addition, the quality of raw materials related to hot stamping must also be guaranteed, such as: the hot stamping suitability of the substrate , the performance of anodized aluminum materials and the quality of hot stamping plates, etc. If there is a problem in a certain link, it will definitely affect the final hot stamping effect.
1. Choose the right substrate
There are many substrates that can be hot stamped, usually paper, such as: coated paper, white board paper, white cardboard, textured paper, offset paper and so on. But not all paper bronzing effects are ideal. If the surface is rough and the paper is loose, such as book paper, poor offset paper, etc., because the anodized aluminum layer cannot be well attached to its surface, the unique metal The gloss does not show up well, or even hot stamping.
Therefore, the hot stamping substrate should be made of paper with dense texture, high smoothness and high surface strength, so as to obtain a good hot stamping effect and fully reflect the unique gloss of anodized aluminum.
2. Select the appropriate anodized aluminum model according to the different substrates
The structure of anodized aluminum has 5 layers, namely: polyester film layer, peeling layer, color layer (protective layer), aluminum layer and adhesive layer. There are many types of anodized aluminum, the common ones are No. 1, No. 2, No. 8, No. 12, No. 15, etc. In addition to gold, there are dozens of colors such as silver, blue, brown-red, green, and red.
When choosing anodized aluminum, it is not only necessary to choose the appropriate color, but also to choose the corresponding model according to the different substrates. Different models have different properties and range of materials suitable for ironing.
Usually, No. 8 is used for hot stamping of paper products, because No. 8 anodized aluminum has moderate adhesion and good gloss, which is more suitable for general printing paper or varnished paper and varnished cloth for hot stamping. If you are hot stamping on hard plastic, you should choose other corresponding models, such as 15-gauge anodized aluminum.
The quality of anodized aluminum is mainly checked by visual inspection and hand feel, such as checking the color, brightness and trachoma of anodized aluminum. Good quality anodized aluminum requires uniform color, smooth after hot stamping, and no trachoma.
The fastness and tightness of anodized aluminum can generally be checked by rubbing it by hand, or sticking to its surface with transparent tape.
If the anodized aluminum is not easy to fall off, it means that the fastness and tightness are good, and it is more suitable for hot stamping small text patterns, and it is not easy to paste the plate during hot stamping; It can be used for hot stamping with sparse pictures and texts; in addition, pay attention to the broken ends of anodized aluminum, the less broken ends, the better.
It is worth noting that the anodized aluminum must be properly stored, and should be stored in a ventilated and dry place. It should not be mixed with acids, alkalis, alcohols, etc., and should be protected from moisture, high temperature, and sun protection. Otherwise, the anodized aluminum will be shortened. Period of use.
3. Make a hot stamping plate
Hot stamping plates generally have copper plate, zinc plate and resin plate. Relatively speaking, the copper plate is the best, the zinc plate is moderate, and the resin plate is slightly worse. Therefore, for fine hot stamping, copper plate should be used as much as possible. For the hot stamping plate, it is required to have a flat surface, clear graphic lines, smooth edges, and no pits and burrs.
If the surface is slightly uneven or slightly scratched or fluffed, it can be gently wiped with refined charcoal to make it smooth and smooth. The depth of the hot stamping plate should be slightly deeper, at least 0.6mm or more, and the slope should be about 70° to ensure that the hot stamping graphics are clear, reduce the occurrence of contiguous films and paste, and improve the print durability.
The design of hot stamping text, lines and patterns is very particular. Graphics and texts should be as moderate in thickness and density as possible. If they are too small or too thin, it will be easy to miss the strokes; if they are too thick and dense, it will be easy to paste.
4. Control the hot stamping temperature
The hot stamping temperature has a great influence on the melting degree of the hot melt silicone resin peeling layer and the adhesive. The hot stamping temperature must not be lower than the lower limit of the temperature resistance range of the anodized aluminum, which is the minimum temperature to ensure the melting of the anodized aluminum adhesive layer.
If the temperature is too low and the melting is not sufficient, it will cause the hot stamping to fail or the hot stamping is not strong, so that the imprint is not strong, incomplete, missing or scratched;
If the temperature is too high, the melting will be excessive, so that the anodized aluminum attached to the print will also melt and fall off, resulting in paste. The surface of the aluminum layer and protective layer is oxidized, which reduces the brightness or loses the metallic luster of the hot stamping product.
Generally speaking, the electric heating temperature should be adjusted between 80 and 180 °C. The larger the hot stamping area, the higher the electric heating temperature; otherwise, it is lower.
The specific situation should be determined according to various factors such as the actual temperature of the printing plate, the type of anodized aluminum, and the graphics and text conditions. Usually, the most suitable temperature should be found by trial ironing, and the clear graphics and text lines should be embossed at the lowest temperature. as standard.
5. To reasonably master the stamping pressure
The hot stamping pressure has a great relationship with the adhesion fastness of anodized aluminum. Even if the temperature is suitable, if the pressure is insufficient, the anodized aluminum and the substrate cannot be firmly adhered, or the phenomenon such as color fading and imprinting will occur; on the contrary, if the pressure is too high, the compression deformation of the gasket and the substrate will be too large, resulting in paste The plate or print becomes thicker. Therefore, the hot stamping pressure should be carefully adjusted.
When setting the hot stamping pressure, you should mainly consider: the properties of anodized aluminum, the hot stamping temperature, the hot stamping speed, the substrate, etc. Generally speaking, when the paper is strong, smooth, the printed ink layer is thick, and the hot stamping temperature is high and the vehicle speed is slow, the hot stamping pressure should be smaller; otherwise, it should be larger.
In addition, similar to printing, attention should also be paid to the liner for hot stamping. For smooth paper, such as: coated paper, glass cardboard, it is best to use rigid liner paper, so that the obtained imprint is clearer; on the contrary, for smoothness For poor and rough paper, the pad should be softer, especially if the hot stamping area is large.
Finally, the hot stamping pressure must be uniform. If it is found that the local hot stamping cannot be applied or the flax is produced during the trial printing, it may be that the pressure here is uneven. You can put tissue paper on the flat plate at this place to make appropriate adjustments.
6. The hot stamping speed should be as constant as possible
The contact time is proportional to the hot stamping fastness under certain conditions, and the hot stamping speed determines the contact time between the anodized aluminum and the substrate.
The hot stamping speed is slow, the contact time between the anodized aluminum and the substrate is long, and the bonding is relatively firm, which is conducive to hot stamping; on the contrary, the hot stamping speed is fast, and the hot stamping contact time is short, and the hot-melt silicone resin layer and adhesive of the anodized aluminum are If it is not completely melted, it will cause the hot stamping to fail or the imprint to become blurred.
Of course, the hot stamping speed must also be adapted to the pressure and temperature. If the hot stamping speed increases, the temperature and pressure should also be appropriately increased.
In addition, the performance of anodized aluminum itself has a great influence on the hot stamping speed. Good quality anodized aluminum can achieve rapid hot stamping, which is quite different from domestic anodized aluminum and imported anodized aluminum.
Domestic anodized aluminum is usually only suitable for low-speed hot stamping, the speed is about 2000 sheets/h, and the highest is generally not more than 3000 sheets/h; imported ones can reach 8000 sheets/h, or even higher. But no matter what the speed is, the important point is that the stamping speed should be kept as relatively stable as possible and not easily changed.
Under the premise of stabilizing the hot stamping speed, the hot stamping temperature and pressure should be properly adjusted to optimize the hot stamping effect, which can reduce the variable factors, make the operation stable, and easily control the hot stamping quality.
The above are just a few main factors that affect the quality of bronzing, and these factors are not isolated from each other, they are mutually restrictive.
Determining these factors should be based on the hot stamping suitability of anodized aluminum and the characteristics of the substrate, and the graphic structure, area and hot stamping speed of the hot stamping plate to determine the best pressure, and finally adjust the appropriate hot stamping temperature.
The basic starting point should be hot stamping with as uniform and moderate pressure as possible, low temperature and relatively stable hot stamping speed, so as to achieve clear and clean pictures, flat and firm, high gloss, no dirty spots, no blisters good effect.
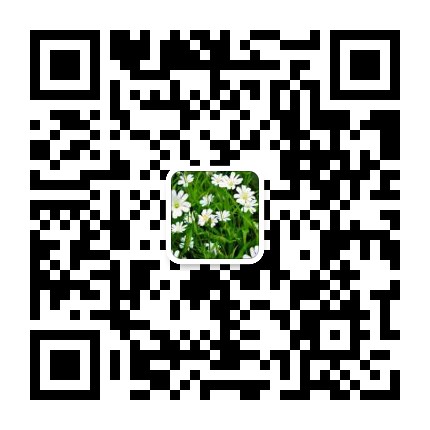
Post time: Sep-05-2022