Industrial rubber rollers should be stored in warehouses with a temperature of 10-35°C and a relative humidity of 50-80%. If the temperature is too high or too low, it will cause thermal cracking or thermal crosslinking of the rubber, which will cause the rubber surface to age, harden, lose its proper elasticity, and crack, resulting in a decrease in wear resistance; The air will cause the roller core to absorb moisture and rust.
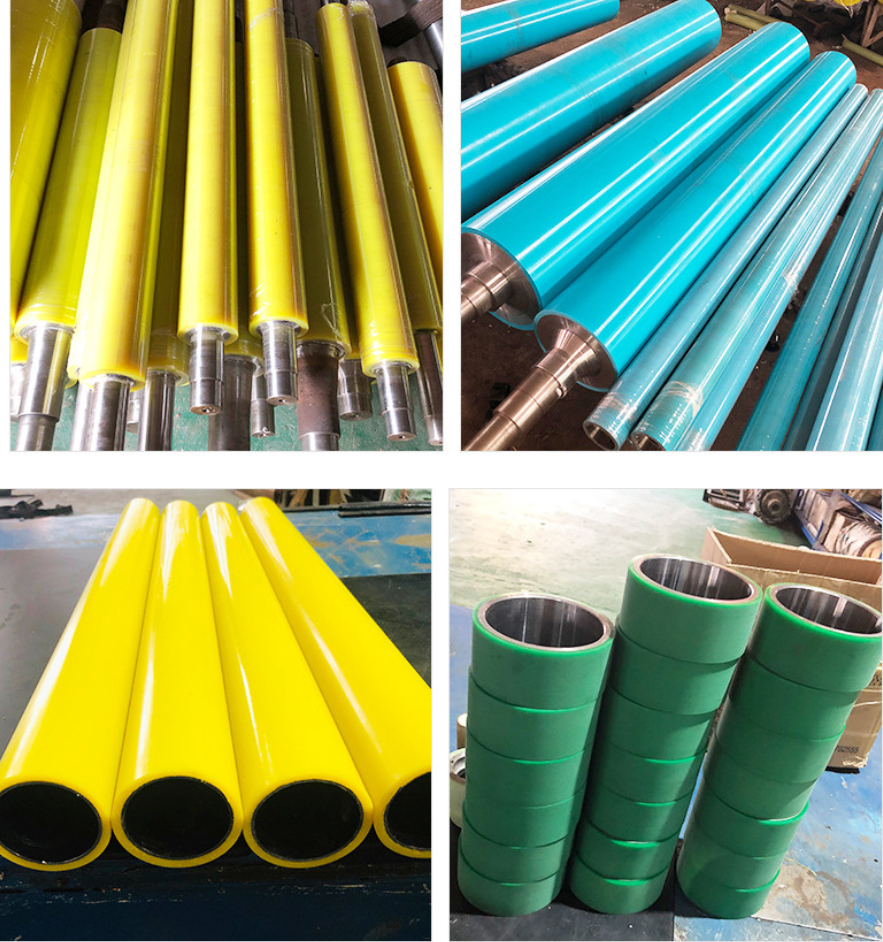
1. Production Process
The first step of mixing is to control the content of each component, the temperature of heating, etc., so that the hardness and components can be relatively stable. After mixing, because the colloid still has impurities, it is not uniform, so it has to be filtered. Filtration not only ensures that the colloid is free of impurities, but also ensures that the rubber roller can be evenly stressed during operation. The step of making rubber rollers and filtering is especially important for high-speed printing machines, so as to prevent expansion or contraction caused by different reasons.
Then heat, pressurize and vulcanize the rubber roller to stabilize the plasticizer, so that once the rubber shrinks during use, the shrinkage can be reduced to a minimum. Through curing, it can become soft and firm without losing its softness, and finally it can transfer ink better.
Finally there is grinding and polishing. Carrying out these two steps must not require a constant constant temperature. Otherwise, if the temperature is too low, some parts will become brittle; if the temperature is too high, the surface of the rubber roller will be easily carbonized, and peeling will occur during printing, which will lead to a decline in the quality of the rubber roller, which does not have its good characteristics and cannot transfer ink well. cause waste. The last two steps are the key to determine the quality of the rubber roller. Although the surface of the rubber roller looks smooth, there are still many small uneven parts on the surface. Grinding and polishing are to make the size of the rubber roller more accurate and the surface smoother, so that its ink transfer performance is better, and the quality of the printed product is higher.
2. Industrial rubber roller storage
Generally speaking, rubber rollers should be stored in a warehouse with a temperature of 10-35°C and a relative humidity of 50-80%. If the temperature is too high or too low, it will cause thermal cracking or thermal crosslinking of the rubber, which will cause the rubber surface to age, harden, lose its proper elasticity, and crack, resulting in a decrease in wear resistance; The air will cause the roller core to absorb moisture and rust.
Since the rubber roller is covered with rubber, during transportation and storage, avoid direct sunlight, rain and snow, prohibit contact with acids, alkalis, oils and organic solvents, and keep away from radiant heat sources 2m away.
Do not place it under strong light and ultraviolet rays. In addition to direct breakage and crosslinking of rubber molecular chains, ultraviolet rays can also generate free radicals due to the absorption of light energy, which can initiate and accelerate the oxidation chain reaction process. The UV light acts as a heating agent. Therefore, it is necessary to cover the rubber roller with thick paper and black plastic cloth to avoid light, otherwise it will cause aging, discoloration, cracking, etc. of the rubber surface, which will reduce the service life of the rubber roller and affect the quality of the printed product.
When the rubber rollers are stored and stacked, the shafts should be supported for storage, and it is strictly forbidden to squeeze and stack, and the distance between the rollers should not be less than 5mm. When transporting and moving, the shaft must be lifted and suspended to prevent the rubber surface from being squeezed, bumped and scratched.
If the new roller is not in use temporarily, please do not unpack it, only take off the wrapping paper before installation, because the wrapping paper can play a protective role.
In addition, the rubber roller should be stored away from high-voltage equipment, motors and other places where ozone may be generated. Because the chemical activity of ozone is much higher than that of oxygen, it is also more destructive. Improper storage can easily lead to ozone cracking. For rubber rollers stored beyond the standard period, check whether there are any defects before use, and only when they are completely intact can they be used on the machine.
3. Selection of industrial rubber rollers
First of all, in addition to product quality, it is necessary to have a good after-sales service when choosing industrial rubber rollers. This is illustrated by the fact that many users choose rubber rollers nearby.
Rubber rollers are vulnerable items, and most users know little about rubber rollers, which means that users need timely and attentive after-sales service from suppliers. If there is no timely after-sales support and no way to effectively solve practical problems, then the service life of industrial rubber rollers will be shortened.
Secondly, many users easily make such mistakes and spend too much time changing the rubber rollers. The original intention of the user is good: replace the rubber roller every 3 months, and use a new product every time, which can improve the quality of the printed matter. But in reality, things often backfire.
The rubber roller and the printing machine are a running-in process. With the use of the rubber roller, new problems will be discovered, and there will be a better solution next time, so as to achieve the best use stage. However, the continuous replacement of rubber rollers has become a shackle to obtain excellent printed matter. Every time a rubber roller is replaced, it must be shut down, disassembled, installed, and debugged.
Before each use, its conductivity must be strictly checked. Handling: During the handling process, the appearance of the industrial rubber rollers is not allowed to be impacted by external force under any circumstances, which will affect the normal use of the rubber rollers.
Loading and unloading: Whenever loading and unloading industrial rubber rollers, care should be taken to avoid scratching the rubber rollers.
Storage: Industrial rubber rollers should be stored upright or supported by journals, and should not be squeezed together. Ozone can damage the surface of the rubber rollers, causing premature aging and cracking of the rubber. In order to protect the surface of the rubber rollers during storage, they must be stored After wrapping, place in a dark room away from potential sources of ozone and protected from heat deformation and moisture.
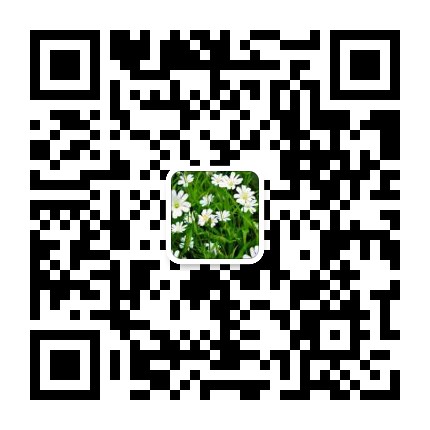
Post time: Jan-06-2023