The manufacturing method of the rubber roller for the An ester rice hulling machine:
The invention belongs to the manufacturing technology of polyurethane products.
In rice processing, the hulling hub (hulling) has only a few years of history of using rubber rollers. The rubber materials used for the rubber rollers are mainly natural rubber, styrene butadiene rubber, etc. However, this kind of rubber roller has high hardness, poor elasticity and unsatisfactory wear resistance. If it is a black rubber roller, the color of rice will turn black when the rice is hulled. If the rubber roller is mainly made of nitrile rubber, the abrasion resistance and temperature resistance will be improved. The first-grade black rubber roller specified by the Ministry of Standards in my country has a tensile strength of >120kg/cm, an elongation at break of >20090, and a wear loss of <1.2Cf113/1.614rn o The polyurethane elastomer molded by casting is one This kind of performance-specific polymer product has the advantages of abrasion resistance, tensile resistance, compression resistance, oil resistance, solvent resistance and high elasticity under high hardness. The service life of the rubber roller of the rice hulling machine made of polyurethane is more than 2.5 times longer than that of the general rubber roller, the breaking strength>300kg/c rr{~, the elongation at break>45090, the wear loss <0.06cin3/i.64m , Shore hardness is 80-90, stable mechanical properties, low temperature rise, output can reach 3810.4kg/h, and rubber consumption is 130.73kg/g, that is, the rubber consumption of processing 130.73kg brown rice is only 19. 8 8.5 jump, this is a considerable improvement for the rice processing industry. The process of making this polyurethane hulling rubber roller is as follows: firstly make polyurethane prepolymer, mix it with chain extender and inject it into the mould, and obtain the product after mould pressing, vulcanization moulding, demoulding and curing.
The purpose of the present invention is to provide a more reasonable and practical manufacturing method based on the existing polyurethane hulling rubber roller production process, so that the product has higher strength, suitable hardness, elasticity and more wear resistance.
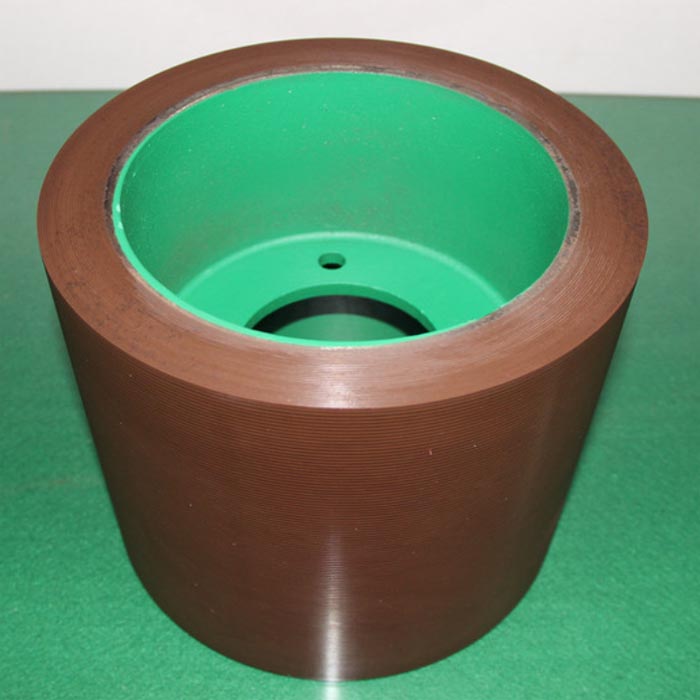
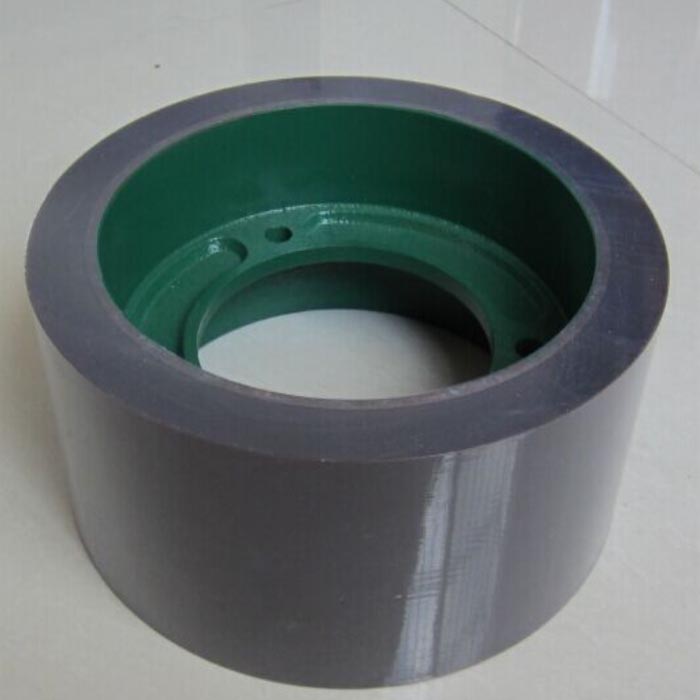
Considering the hulling, strong abrasion resistance is required. Polyester (also known as polyester polyol) is made by the condensation of dihydric alcohol and dibasic acid. It is a macromolecule with a considerable number of hydroxyl and carboxyl groups. The molecular weight of the polyester required by the present invention is 15000-18500, and the hydroxyl value is It is 40~100mgKOH/g, and the acid value is 0.5~3. OmgKOH/g, water content <0.2%p, it must be used at 120~140℃, ≤7. Okpa is dehydrated under vacuum. The general formula of diisocyanate is: OCN-R-NCO commonly used is TDI (toluene diisocyanate, isocyanate is 2.4 and 2.6 difference), the present invention uses pure 2.4 to 24/26=80/2 0; Sometimes the present invention also uses part of MDI (diphenylmethane-4,47-diisocyanate). Polyester is cooled to 40-60 after dehydration. At C, add diisocyanate and make the reaction proceed at 80-88°C for 1 to 2 hours. After the reaction is completed, samples should be taken to analyze the amount of -NCO contained therein. The present invention designs this prepolymer to contain-NCO is 3~10, In order to further react with the chain extender to generate polymer elastomers. After the reaction is completed, take a sample for analysis-NCO content, the prepolymer needs to be placed at 110~120. C, ≤7. Degas under Okpa vacuum for 20 to 60 minutes, and then combine the measured degassed prepolymer and the chain extender calculated according to the prepolymer analysis-NC O content at 80 to 90. Mix and stir uniformly at C, and pour it into the mold core. The mixture will gradually thicken into a gel due to the chain growth reaction. Close the mold and press it into the vulcanization box, 120-130. C Vulcanize for 1 to 3 hours, remove the mold, and place the vulcanized rubber roller at 70 to 90. Cured for 8-12h under C condition, and cut the edge to become the finished rubber roller.

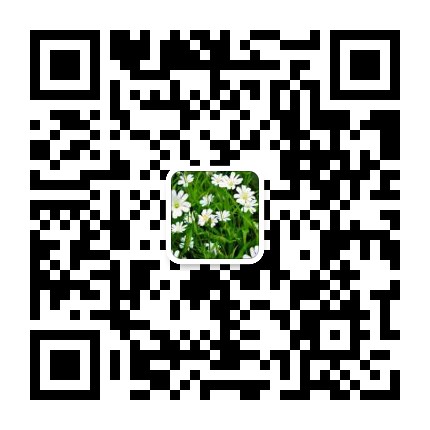
Post time: Jun-17-2021