The rubber roller is a roll-shaped product made of metal or other materials as the core and covered with rubber through vulcanization. The rubber roller is used for processing hot-adhesive products, such as polyethylene calendering, embossing, printing and dyeing, film and fabric coating adhesives, plastic composites, using its high temperature resistance, ozone resistance, chemical inertness and non-adhesion to plastics. , Corona treatment and other machinery are also used as the release roller on the sugar production and packaging machine and the manufacture of non-woven fabrics.
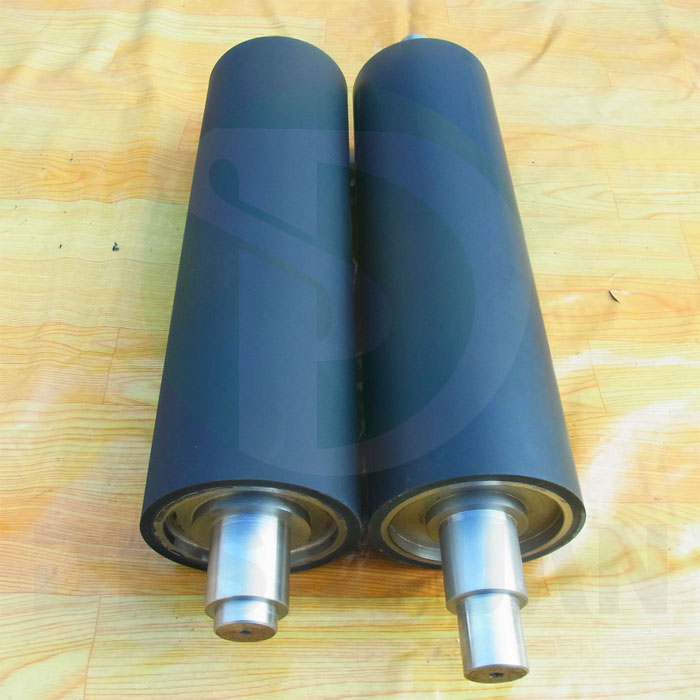
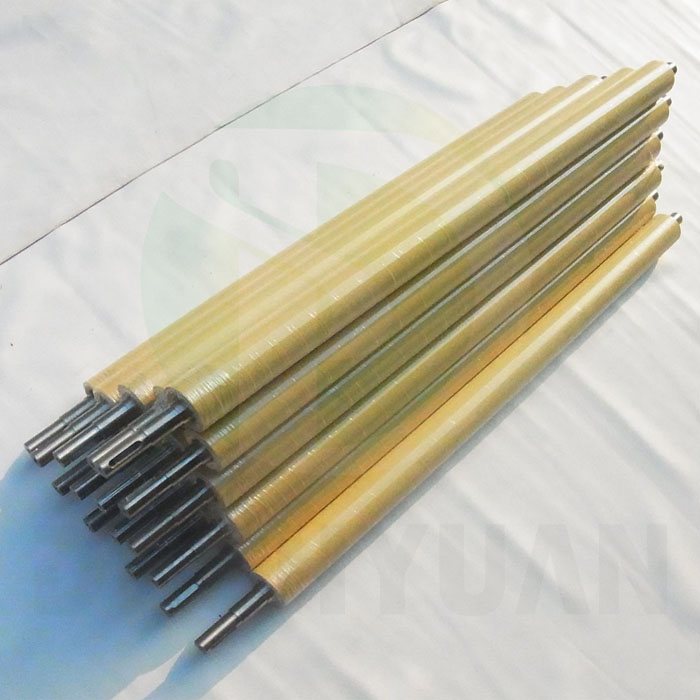
The manufacturing steps of the rubber roller:
Main raw materials: polymer, vulcanizing agent, plasticizer, filler, accelerator
The main process flow and function: mixing-filtration-curing treatment-grinding-polishing
1. Mixing: Control the content of each component, heat-bake temperature, etc., to stabilize the hardness and composition.
2. Filtration: Make the colloid uniform and free of impurities. This is particularly important for high-speed printers: even in high-speed operation, the force is uniform, and the transmission energy is uniform. When expansion or contraction is caused by various factors, it can still maintain uniformity, so that only adjustments can reduce or avoid adverse effects.
3. Curing: Through heating, pressurization and vulcanization treatment, the speed agent is stabilized, and the shrinkage of the rubber is minimized when subjected to external force. Turn the soft and extensible compound into a solid and soft material, which is more suitable for ink transfer and transfer.
4. Grinding and polishing: the key to determine the dimensional accuracy and surface area of the rubber roller, especially the arc treatment of the alcohol water roller. The rubber surface looks smooth, but under a high-power magnifying glass, there are many small protrusions and depressions. These convex and concave parts increase the surface area of the rubber roller, making it have superior ink transfer and transfer performance.
This process requires constant temperature: if the temperature is too high, the surface is easy to be carbonized, and the phenomenon of peeling will appear when printing in a short time. If the temperature is too low, it is easy to be embrittled locally, causing the ink transfer performance to decrease.
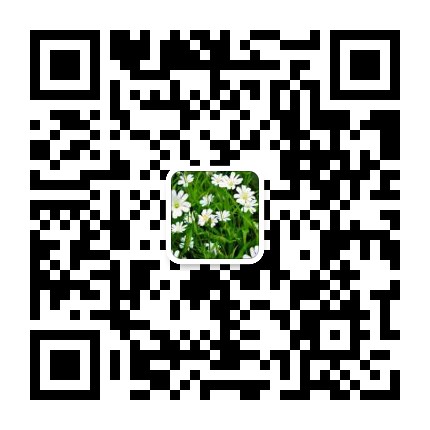
Post time: Jul-20-2021