1. Rubber Production
Standard rubber roller manufacturing involves a rubber fabrication step, which can be achieved either by plying method, extrusion, casting, or die press.
Plying involves the calendering process, during which, to make calendered rubber sheeting, rubber is passed through a combination of rollers. As the rubber sheet moves through the rollers, it is smoothed and flattened. Using this process, two types of polymer can be sandwiched together, if an application demands. Once the calendared sheet is ready, the sheet becomes a rubber cover of an iron core or another metal core. With that, it is a rubber roller. Based on client requirements, sheets can be polished, glazed or embossed.
Extrusion is the most common manufacturing method that involves an extruder. With this method, a rubber profile of fixed cross-sectional can be made continuously by-passing rubber through a die. In this process, raw material is heated by passing it through a screw mechanism, which heats material by a combined action of pressure and temperature, and then the material is pushed through the die. The critical step in this fabricating technique is curing, which involves conditioning the rubber product in a controlled environment where it is exposed predetermined temperature and pressure. The curing process gives the structural strength to a rubber product by removing porosity.
Casting, inarguably, is the oldest way of giving shape to a range of materials. From automobile engines to high-end sculptures, have been crafted by this method. Whatever the material is, all is molded by a same principle, which involves pouring of raw material in a mold and then exposing it to an oven for a period of time that cures it and set it in a predefined shape.
Die press rubber fabrication commonly involves a hydraulic press and a die. The die gives the shape to the raw rubber, whereas press provides pressure and heat to cure the rubber product. The process begins by filling raw rubber into a metal mold, and then a hydraulic arm fitted with a die presses the mold and provides heat and pressure. Unlike extrusion, the press method is not continuous, thus is not as efficient as extrusion.
2. Roller Manufacturing
Rubber rollers are usually manufactured via casting or molding, but they may also made through extrusion.
Casting processes are utilized only with rubber rollers that have metallic cores. In this case, cores are formed through a metal casting process like stamping, after which they are bound to a rubber coating. Binding is carried out using a bonding agent that usually made of polymer-solvent solutions, a primer coat based on phenolic-style resins and a top layer of mixed polymers and other various materials.
Rubber roller molding processes include compression molding and injection molding; these are used for solid rollers.
Extrusion of rubber rollers takes place when manufacturers heat chosen elastomeric material(s) and squeeze the molten material through a die that has a pin in the center to fabricate the hollow tube.
3. Grooving
The next step involves surface grooving. There are a number of grooves that can be created on a surface of rubber, including square, trapezoidal, “V”, double edge saw, half circle, and round. Moreover, on a rubber roll, these grooves can be made vertically, horizontally, helically, worm, diamond cut groove and screw threaded.
4. Inspection
At the end of this step, the products are inspected for aberration.
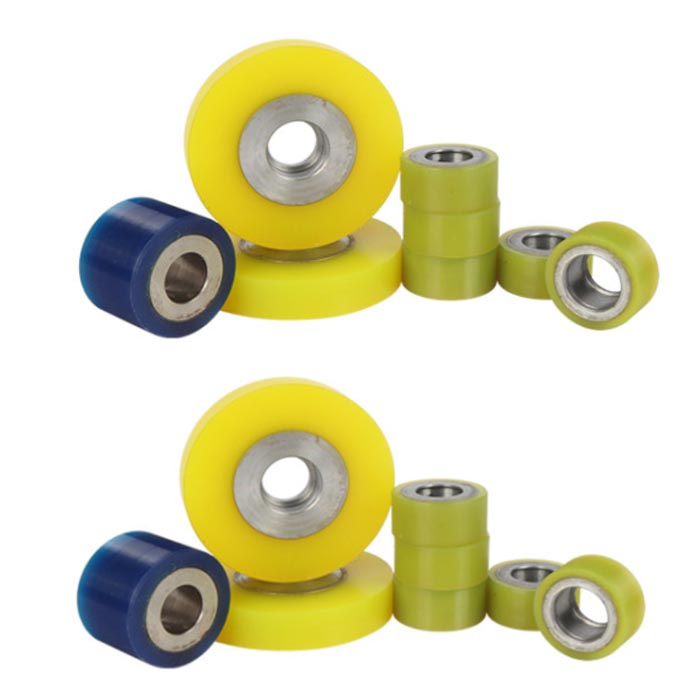
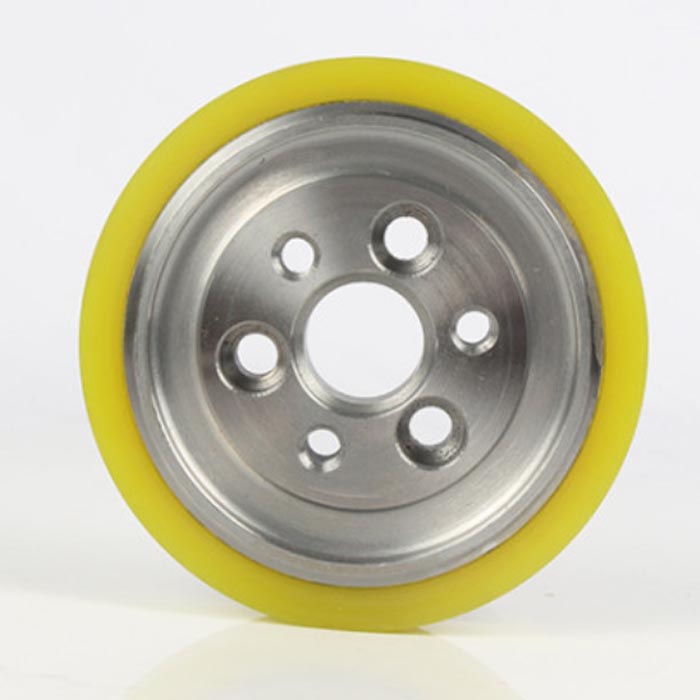
Standards
Rubber rollers are subject to a number of different standard requirements, depending on their application. For example, rubber machinery like extruders, generally speaking, any rubber roller you purchase should meet ISO standards for rubber products.
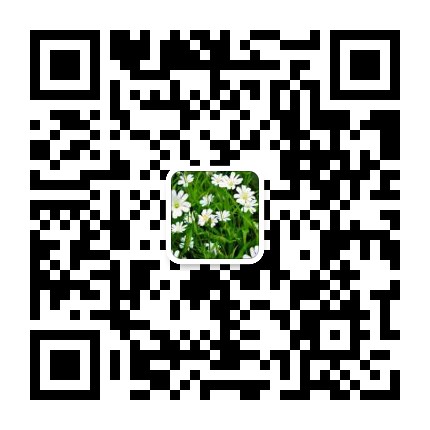
Post time: Apr-16-2021