The life of the rubber roller
The life span of the rubber roller is not only related to the raw materials used in the production process, but also has a great relationship with the maintenance in daily life. If you do not pay attention to maintenance and maintenance, no matter how good the rubber roller is, it will break down very quickly. What could have been used for several years may be broken after a year. If you pay attention to daily maintenance and maintenance, use 2-3 Years are not a problem. Of course, during the operation, you should also pay attention to the operation step by step according to the instructions for use, often check the use of the rubber roller, and after use, handle it gently, put it in a suitable place, and choose a good storage environment.
The process of rubber roller coating processing needs to follow a certain process, as follows:
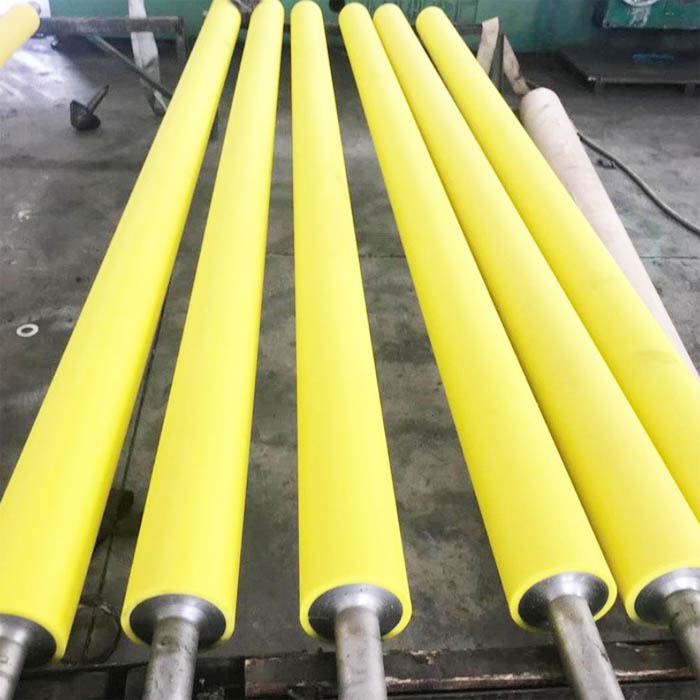
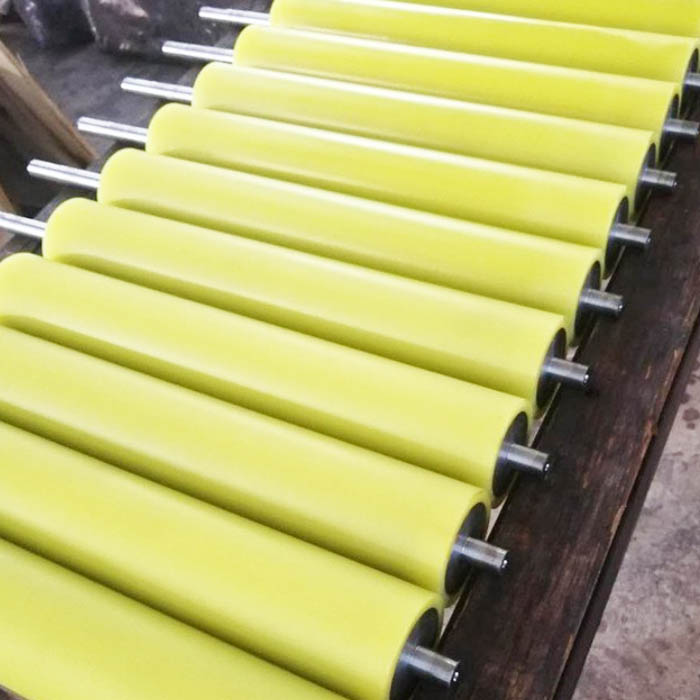
1. Cleaning the rubber roller core: If it is a new rubber roller core, the oil on the surface of the core needs to be cleaned with a cleaning agent; if it is an old rubber roller core, it is necessary to remove the outer coating of the old rubber roller. At the same time, use the cleaning agent to clean the remaining glue on the surface of the iron core.
2. Rough surface treatment of the iron core of the rubber roller: roughen the surface of the iron core of the rubber roller to increase the bonding area between the iron core surface of the rubber roller and the lagging.
3. Sandblasting treatment: sandblast the rough treated rubber roller core, and sandblasting will select different types of sand according to the material of the rubber roller core for sandblasting. The purpose of sandblasting is to make the surface of the rubber roller rougher, and the glue and the iron core will be better bonded after rubberizing.
4. Lagging: The rubber roller iron core after the above treatment is covered according to the customer's requirements, and different covering materials meet different requirements, such as: rubber-covered ink resistance is good, polyurethane rubber-covered wear resistance The pressure resistance is good, and the high temperature resistance of the silica gel is good.
5. Rubber roller vulcanization: The rubber roller generally needs a vulcanization time of 10-15 hours after vulcanization. After vulcanization, the rubber roller iron core and the rubber cover will be tightly bonded, and a rubber-coated rubber roller will be formed.
6. Cots grinding: Grind according to the size and shape required by customers. When some customers have higher requirements on the surface of the rubber rollers, it is necessary to use a CNC grinder to mirror the rubber rollers.
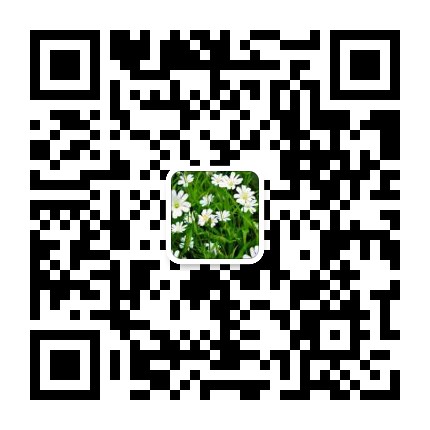
Post time: Jul-06-2022