The printing rubber roller has moderate hardness and elasticity, high oil resistance, washing solvent resistance, abrasion resistance and shape stability. Soft rollers are generally made of SBR, CR and PU. The surface of the hard rod was originally made of copper and later replaced by polyester resin.
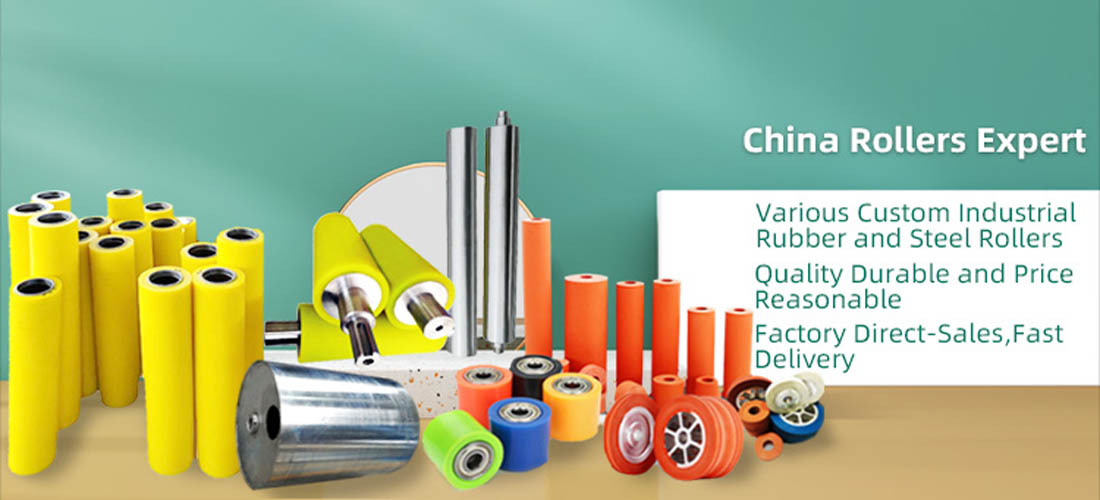
Repair of printing rubber roller
In the work project, the printing rubber rollers usually appear, wear and tear, and so on. If the new roller is replaced, the cost is too high and the production schedule will be affected. Rubber repair agent can be used for repair. The repair process, take the BD916 rubber repair agent produced by DECAI Factory as an example:
1. Surface treatment: clean, decontaminate, degreas, and dry the touch hair to be repaired.
2. To repair with glue, pour the rubber repair agent curing agent B group into the main agent A group iron cans and quickly stir evenly (A:B=1:1), then pour it to the area to be repaired and smooth it.
3. Curing: curing at room temperature for 4-6 hours can be used, 48 hours to reach the maximum strength.
The key to offset printing technology is the control of the balance between water and ink channels, and the balance of ink and water relies on the key components of rubber rollers and ink rollers, the quality of which can directly affect product quality. This is especially true for gravure, embossing, and flexo printing. General printing companies have to maintain equipment once a week, including the maintenance of printing rubber rollers.
There are several ways to maintain the printing rubber roller:
1. To clean the printing rubber roller, you must use designated chemical agents, such as industrial alcohol, etc., and must not use corrosive solvents;
2. The rubber rollers should be cleaned carefully after the daily production operation is completed, and washed twice;
3. The surface of the printing rubber roller should be wrapped in newsprint and placed in a ventilated and dark place.
4. Take off the rubber roller during holidays to prevent deformation under pressure;
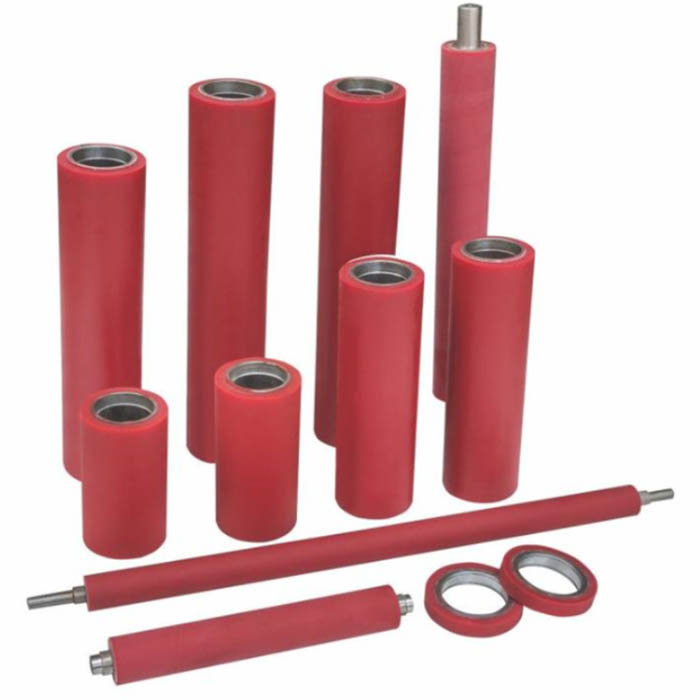
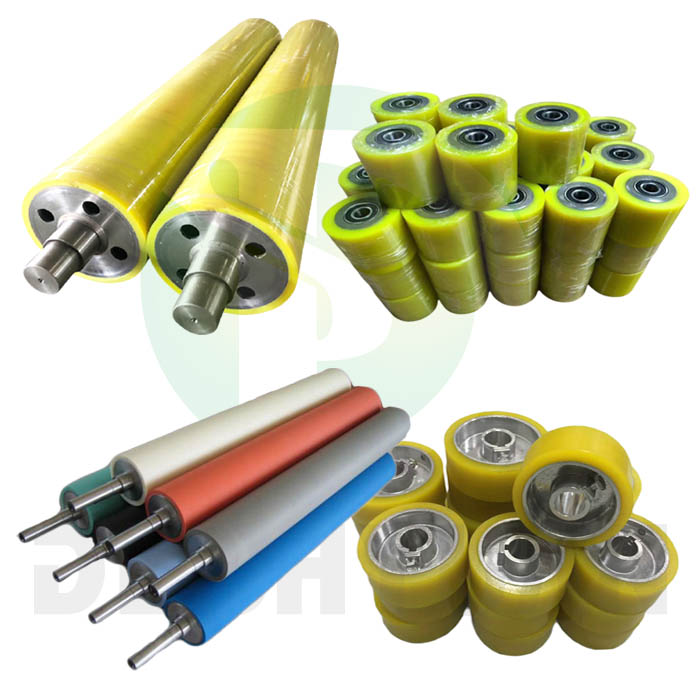
How to keep the rubber roller?
(1) After the rubber roller has been stored for 2 to 3 months, the direction should be changed to prevent bending and deformation when placed in one direction for a long time, and pay attention to prevent the shaft head from rusting.
(2) It is necessary to make a spare rubber roller, but it should not be used for too long, because the spare rubber roller will naturally age and take up capital. It is necessary to prevent the occurrence of phenomena such as aging of the adhesive layer, wrinkles, and rust of the shaft head caused by storage for too long.
(3) The rubber rollers stored for a long time should be ground or wipe the surface of the rubber rollers with pumice powder before use.
(4) The rubber roller should be stored in a cool, dry and ventilated place, and it should be in a vertical or horizontal state.
(5) When stored horizontally, it should be placed on a shelf. The glue surfaces should not be stacked or squeezed to prevent the glue surfaces from deforming and sticking under pressure.
(6) Avoid storing it with acids, alkalis, oils and sharp substances to avoid corrosion and damage to the rubber rollers.
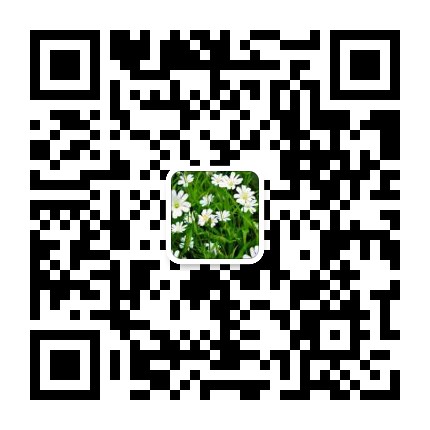
Post time: Aug-03-2021