In the work project, the printing rubber rollers usually appear, wear, and break holes. If a new roller is replaced, the cost is too high and the production schedule will be affected. It can be repaired with rubber repair agent.
Mending process, taking the BD916 rubber mending agent produced by Xiangfan Lianji Adhesive Factory as an example:
1. Surface treatment: The printing rubber roller is to be repaired and touched, cleaned, decontaminated, degreased, and dried.
2. For repairing with glue, pour the printing rubber roller repair agent curing agent B group into the main agent A group iron cans and quickly stir evenly (A:B=1:1), then pour it to the area to be repaired and smooth it
3. Curing: It can be used after 4-6 hours of curing at room temperature, and the maximum strength is reached within 48 hours.

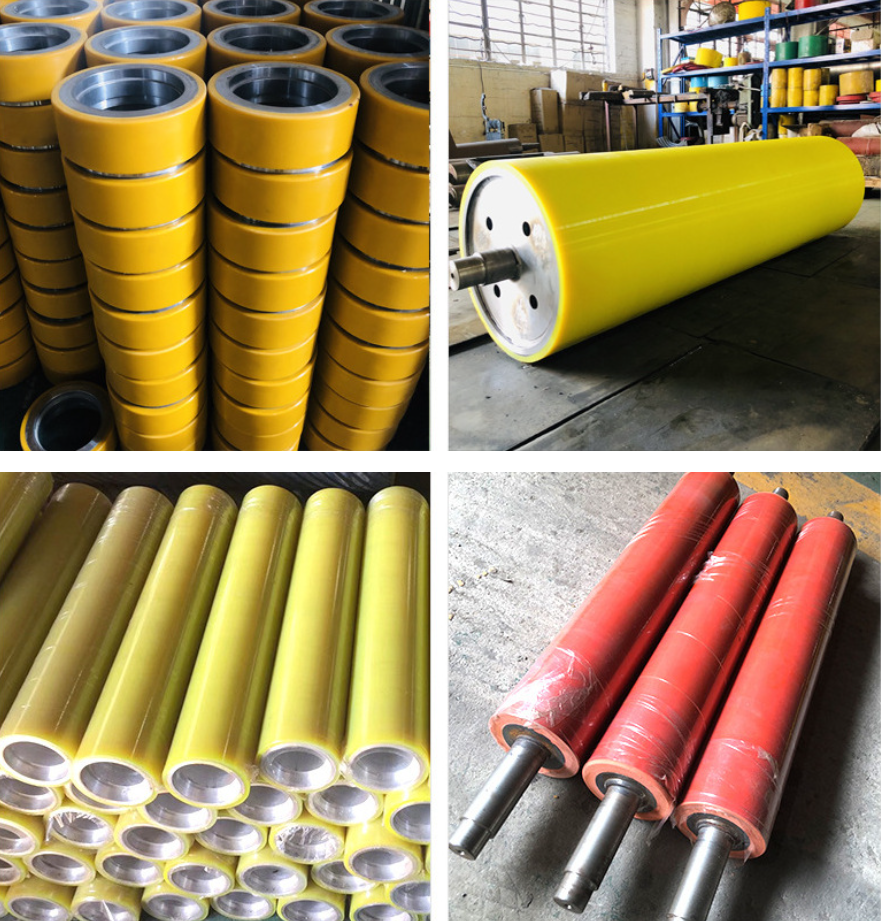
Rubber preparation of rubber roller production process
For rubber rollers, the mixing of rubber is the most critical link. There are more than 10 kinds of rubber materials for rubber rollers ranging from natural rubber and synthetic rubber to special materials. The rubber content is 25%-85%, and the hardness is soil (0-90) degrees, which spans a wide range. The conventional method is to use an open rubber mixer to mix and process in the form of a variety of master batches. The so-called rubber mixing machine is a rubber mixing machine with exposed rollers used in the rubber factory to prepare mixed rubber or to heat, plasticize, and mold the rubber. But these are a kind of mixing plastic equipment. In recent years, companies have increasingly switched to intermeshing internal mixers to prepare rubber compounds by means of segmented mixing.
After the rubber material is uniformly mixed, it is necessary to filter the rubber with a rubber filter to eliminate impurities in the rubber material. Then use a calender, an extruder, and a laminating machine to make a film or strip without bubbles and impurities for the rubber roller forming. Before molding, these films and strips must be subjected to strict appearance inspections, and the fresh surface should be kept to prevent adhesion and extrusion deformation. There should be no impurities and bubbles in the rubber on the surface of the film and strip, otherwise blisters may appear when the surface is polished after vulcanization.
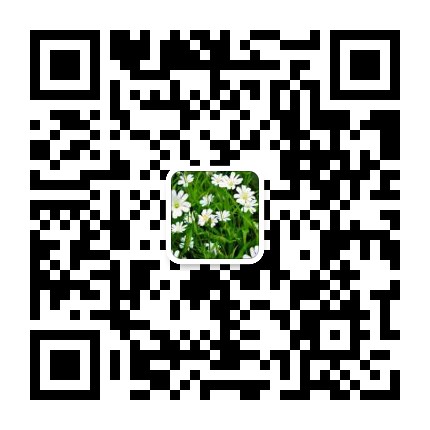
Post time: Jun-28-2021