The rubber roller is an important part of the printing machine, which has an important influence on the quality of printed products. How to choose high-quality, high-performance printing rubber rollers is of great significance for improving the production efficiency of iron printing plants, meeting various requirements of customers, and ensuring the quality of iron printing products. With the development of my country's metal packaging industry and the wide application of various iron-printing products, the market has various demands for iron-printing products, which undoubtedly puts forward higher and higher requirements for the quality of iron-printing products. At the same time, the performance, speed and accuracy of the iron printing machine are constantly improving, which puts forward different requirements on the variety, grade and quality of the rubber roller of the iron printing machine.
The rubber roller is easy to clean. It is very easy to switch between dark and light inks in production. As the plate roller of some printing presses, it can stick dust and other dirt on the printing plate without frequent loading and unloading cleaning, which is convenient for production.
The heat of the rubber roller will accelerate the desulfurization, produce thermal aging, make the surface sticky, soft, and even cracks into orange patterns. The rubber roller can only be replaced at this time.
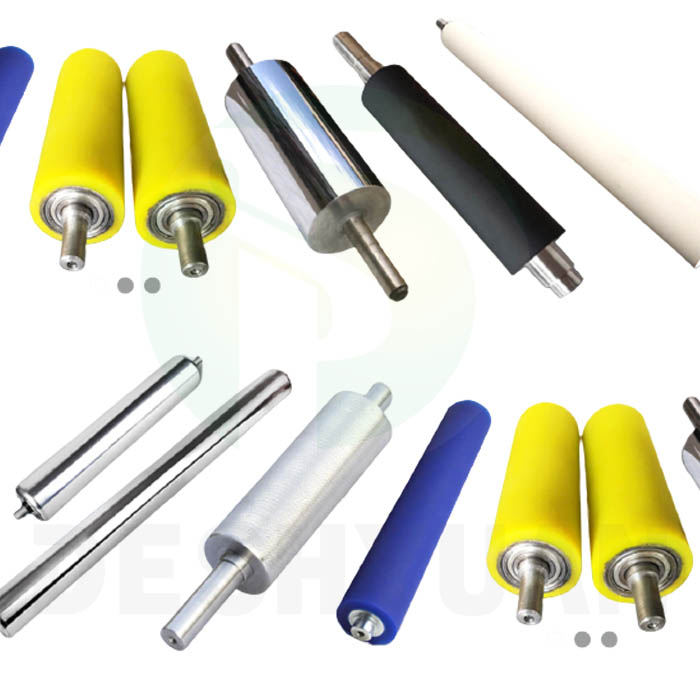
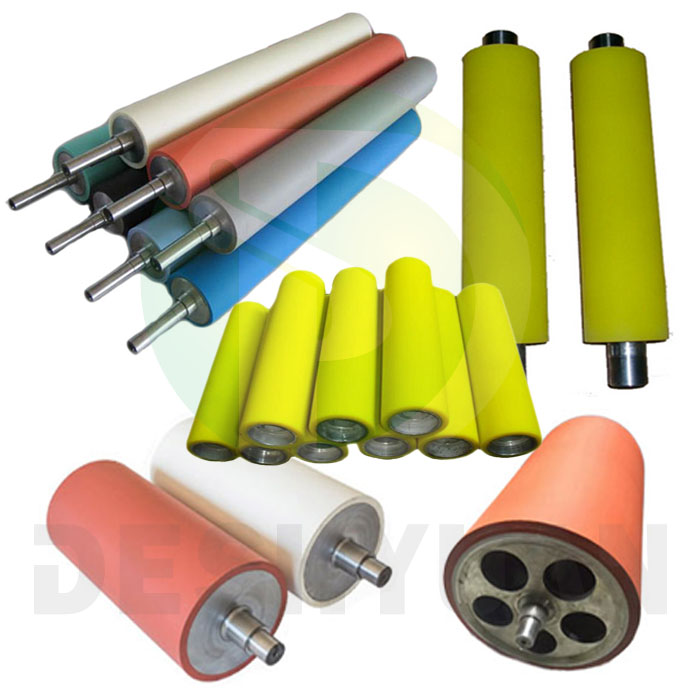
There are many details that should be paid attention to in the process of rubber roller application, which is briefly described as follows:
1. When turning on the heating, check whether the silicone roller rotates normally. When turning off, the residual temperature delay should be set too fine to see whether it is normal, and it cannot be turned off directly (the residual temperature delay is usually set at 40-50 minutes);
2. In the process of dullness, if there is a sudden stop due to power failure or other reasons, you should immediately wear gloves, and remove the rubber roller while rotating it and put it in another place to dissipate heat, so as to avoid uneven heat from burning the silicone Roll
3. When changing the rubber roller to tighten the silica gel, wait until the silica gel is heated to the required temperature before locking it firmly, but not too tight;
4. Silicone rollers should usually be kept clean, even if the transfer film debris is prevented from sticking to the rubber roller's appearance, if the appearance has dirt, it can be cleaned with cloth processing alcohol. If there is stubborn dirt, sand it with fine sandpaper.
5. Like other printing rubber rollers, silicone rollers should not collide with other hard objects (such as wrenches) or squeeze them when they are used or stored. Keep away from corrupted items;
6. The temperature of the silica gel can be transferred normally at about 190 degrees. In the environment where the product transfer is qualified, the pressure and temperature of the silica gel roller should be reduced.
Post time: Oct-27-2020