Cold rolling mill roll: Rolls used for cold rolling are generally flat rolls for rolling sheets and strips. Cold rolls in a broad sense include work rolls that are in contact with the rolling stock and backup rolls that support them. Because backup rolls are self-contained, cold rolls are often referred to in a narrow sense as cold work rolls. The cold roll must have sufficient strength, uniform high hardness and surface quality to withstand extremely high rolling force, ensure sufficient wear resistance, and meet the requirements of rolling precision. Forged steel rolls that can be hardened to high hardness are used as cold rolls.
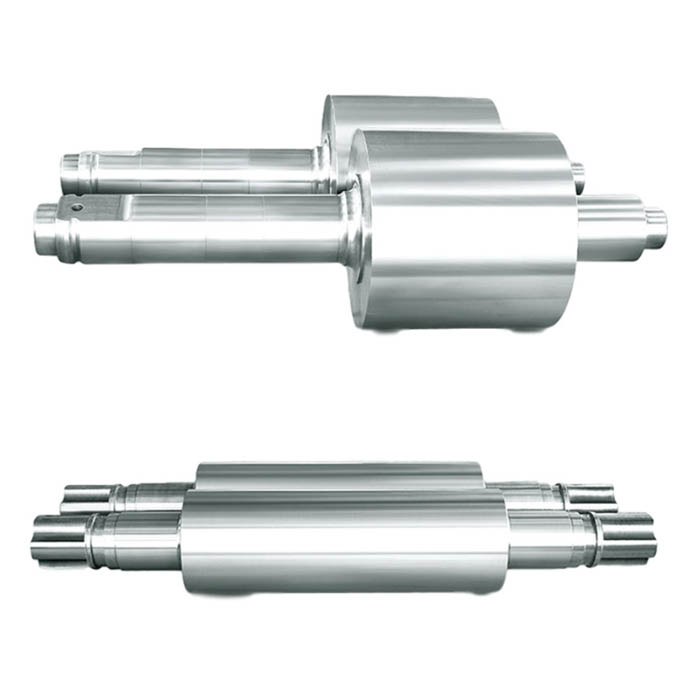
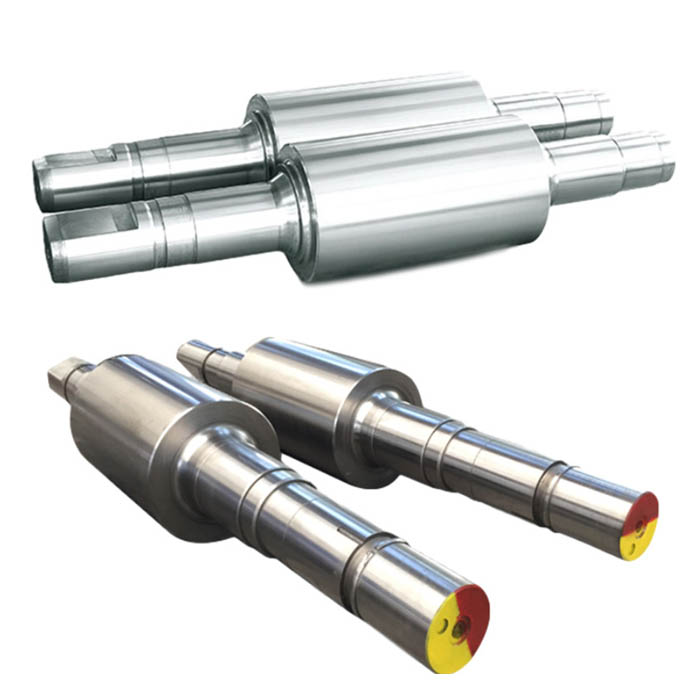
1. Application of cold roll texturing technology
Baking process: increase the rolling friction and increase the bite angle
Intermediate rolling process: improve friction conditions, prevent slippage (slip between rolls), and prevent annealing from sticking
Flattening process: production of matte steel sheet for stamping
2. Various cold roll texturing methods and characteristics
There are problems with the main characteristics of the processing principle of the texturing method
Grinding wheel grinding hard particles with furrow effect is easy to process, low in cost, poor in texturing effect, and reduces roll life
Shot peening, high-speed impact of hard particles, random texture, surface mechanical deformation, poor roughness control accuracy, associated waviness, noise and dust pollution
EDM texturing tip discharge ablation has high texturing efficiency and better roughness accuracy, and the morphology effect is better than shot peening
Laser Texturing Pulsed laser has good effect of fast melting and texturing, has modification and strengthening effect, high roughness accuracy, and energy conversion efficiency is inferior to that of electric spark and electron beam.
Electron beam texturing Electron beam pulse fast melting and texturing effect is good, processing efficiency is high, there is modification and strengthening effect, high roughness accuracy requires vacuum conditions.
3. Principle of laser texturing of cold rolls
The surface of the material is acted on the surface of the material by the laser pulse point-like according to the set dispersion
Localized melting/vaporization of material surfaces through photothermal conversion
The required microstructure of pits and hulls is formed by the accumulation of melts by means of aerodynamic relocation
Rapid condensation of melt to obtain modification and strengthening effect
Through the tensile stress generated by the fused structure, the strong stress field of the roll surface is relieved, and the fatigue performance of the roll surface is improved
4. Laser texturing effect:
Better than shot peening (blanking process) in increasing friction and bite angle;
Reduce rolling mill vibration, increase rolling speed, improve shape and product surface quality, and prevent coil annealing and bonding (cold rolling process);
Production of metal sheets with excellent surface quality and stamping performance, such as rough panels with different roughness and mirror panels with good forming performance (flattening process);
Extend the service life of the roll or the excess steel amount in the cycle;
Disperse and dissolve geometric defects on the surface of the billet and improve the yield.
Carbide rolls are mainly used for flattening steel wires in the field of cold rolling to produce flat steel wires or hairsprings. In view of the high hardness and wear resistance of cemented carbide, cemented carbide rolls can roll out high-precision and high-surface quality rolled products, so they are also suitable for rolling foils.
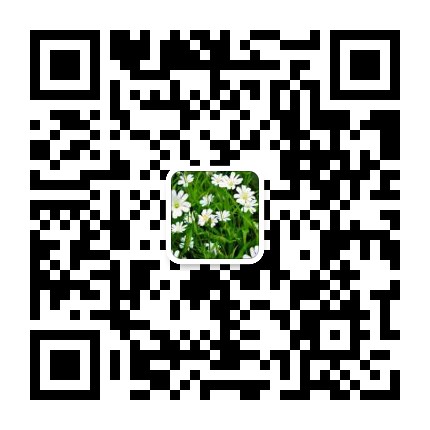
Post time: Mar-14-2022