The traditional back-up roll material is mostly 9CR2M, with a carbon content of about 0.9%, a Cr content of 2$, and a small amount of Mo. This material is a typical cold-rolled work wonton material, which can be obtained after heating and severe cooling. High surface hardness and certain wear resistance. In the past production of forged steel rolls, since there is no special supporting short material, this material is often used as a supporting shaft after quenching and tempering to medium and low hardness. However, with the improvement of rolling mill design requirements and the change of rolling conditions, the deficiencies of this material began to manifest. These changes include:

1. Deeper hardened layer depth requirements. Modern rolling mills often require the unilateral depth of the working ravioli to be above 25 mm, at most 50 nlm, and the unilateral depth of the backup roll is more than 35 mm; at most 75 mm. Due to the influence of its own alloying element content, the hardenability of 9Cr2Mo cannot meet such a requirement.
2. Changes in working conditions require special materials to adapt. Modern rolling mills have higher and higher requirements for rolls. The work series requires wear resistance, accident resistance, roll mark resistance, and high uniformity. The surface of the backup roll requires fatigue resistance and wear resistance. It becomes more important. Due to the high carbon content of 9Cr2M, there are more carbides in the matrix. If these carbides are not handled properly, the distribution
If the state is not ideal, the fatigue strength of the matrix will be reduced; in addition, the Cr/C ratio in the material determines that the carbide of the material is MC3 type, the hardness is low (about 900Hv), and the contribution to the light rolling wear resistance is not enough.
Based on the above situation, the roll manufacturer will work with the design and user to improve the material. The MC3 and MC5 materials of the work rolls have become the mainstream materials of cold-rolled work rolls; the 70Cr3Mo series has also become the preferred material for backup rolls. In some high-speed heavy-duty rolling mills, the back-up roll materials even use 50Cr4MoV and 45Cr5MoV series materials. overall development trend
The potential is a higher alloying element content (mainly Cr, and also adjusted for Ni, Mo) and a lower carbon content. Of course, there are corresponding process improvements from the manufacturer to achieve deeper hardened layer depth, better fatigue resistance and wear resistance, and uniformity of surface hardness.
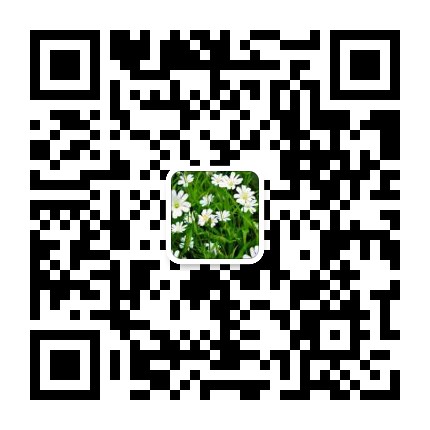
Post time: Mar-28-2022