DECAI is a professional manufacturer of various rubber rollers, rubber rubber rollers, printing rubber rollers, PU rollers, polyurethane rubber rollers, rubber rollers, PU rubber rollers, ink rollers, alcohol rollers, etc., rubber roller factory Tel: 13456489912 Sophie welcomes customers to call , We will serve you!
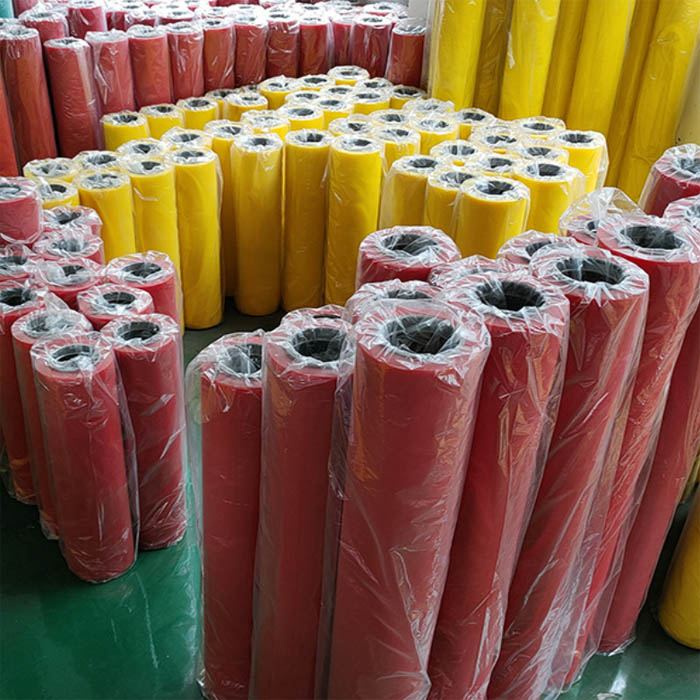
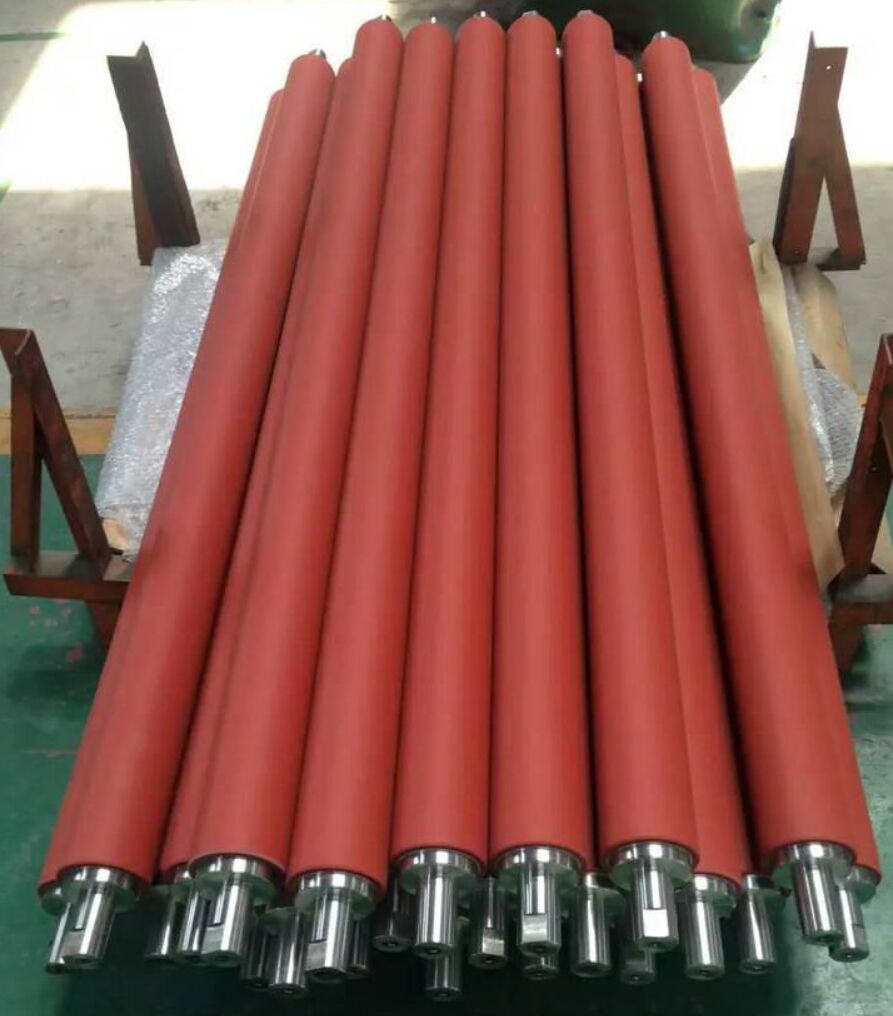
When the rubber roller is stopped, the plate rubber roller should be separated from the printing plate cylinder in time to prevent static pressure deformation. The rubber roller should be taken off during holidays.
(1) After printing every day, clean the ink on the rubber roller carefully. When cleaning, you should choose a special cleaning agent. Never use solvents that are corrosive to the rubber roller. Check whether there is any paper lint, paper powder, paper lint, and paper powder on the rubber roller. It needs to be wiped with a cloth. If it is not cleaned frequently, the surface of the rubber roller will be uneven, deformed and cracked, which will seriously affect the smooth progress of printing and the quality of printing.
(2) Keep the rubber roller shaft head and bearing well lubricated
The accuracy and quality of the shaft head and bearing of the rubber roller directly affect the effect of ink transfer and ink application. If poor lubrication causes the rubber roller shaft head and bearings to wear and gap, it will inevitably lead to the disadvantages of ink application and ink distribution. At the same time, it will also cause the rubber roller to jump, slip and other undesirable conditions, causing the printed product to have water bars and ink bars. Therefore, always pay attention to the wear of the rubber roller bearings, and replace the severely worn bearings in time.
(3) The influence of workshop environment on rubber rollers
For production in humid and sultry weather or in a dusty environment, the adjustment and operation of the machine will cause the surface temperature of the rubber roller to continue to rise, heat and expand, increase the friction of the rubber roller, and shorten the life of the rubber roller, so it is best to Air conditioning is installed in the offset printing workshop.
(4) Deinking
In the offset printing operation, the ink emulsification occurs due to the "large water and large ink", forming a hydrophilic foundation on the smooth rubber roller, and deinking will occur again. The solution is to shovel the emulsified ink, wash the deinking roller with gasoline, and polish the surface with 5% sodium hydroxide aqueous solution and talc to remove the hydrophilic layer, so that the ink roller can restore its lipophilic characteristics. At the same time, the metal rollers (or hard rollers) are also dealt with accordingly. Hard rollers can also be polished with fine water sand under water, but the same part cannot be polished to avoid damage to the rubber rollers.
The ready-to-use rubber rollers should be cleaned, wrapped in paper, and placed on the rubber roller rack. Do not pile several of them together or stand by the wall in order to avoid undue damage to the rubber; the rubber rollers are being sent for processing and casting During the transportation process, remember to throw or press hard, and the roller core must be kept from eccentricity and bending to ensure the normal use of the roller core.
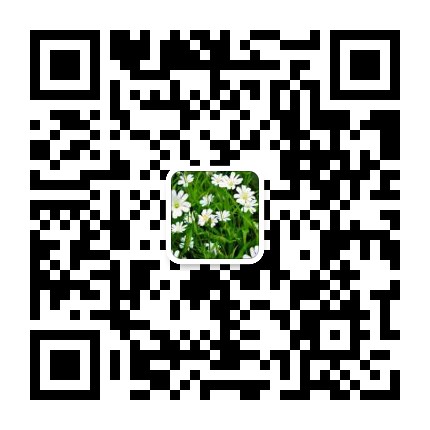
Post time: Aug-16-2021